

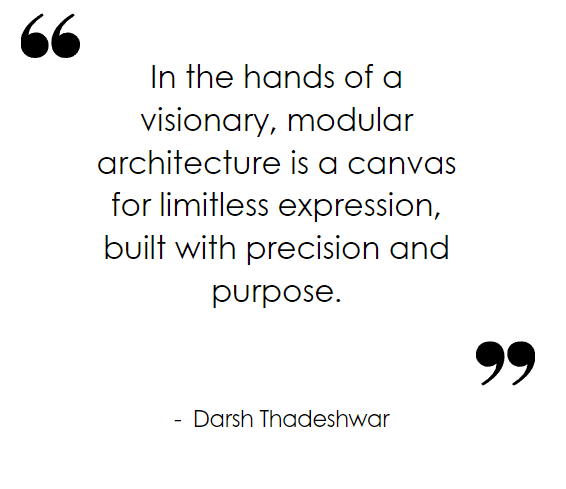
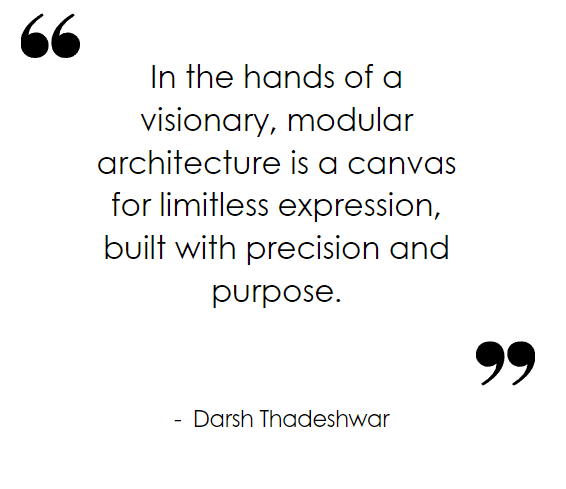
The new wave of modular architecture is reshaping how we build, offering a fresh approach that’s both practical and innovative. Unlike traditional construction, where everything happens on-site, modular architecture starts in a factory. Here, sections of a building, known as modules, are crafted with precision before being transported to the site for quick assembly. This method isn’t just faster; it’s also more efficient, reducing waste and often cutting costs. As cities expand and the need for housing grows, modular construction provides a timely solution that can be rolled out quickly without compromising on quality.
The most important factor that makes this new wave exciting is its adaptability? Modern modular designs aren’t one-size-fits-all, the high co-efficient of customization allow for the creation of unique structures, tailored to specific needs. Whether it’s adding, removing, or reconfiguring modules, the design can evolve with respect to its environment.
Technology has been a game-changer in this space, driving the evolution of modular architecture. With advances in manufacturing, digital design, and eco-friendly materials, the possibilities are expanding. We’re seeing modular techniques applied to everything from high-rise buildings to hospitals, proving that this approach isn’t just versatile but scalable too. Sustainability is at the heart of this movement. By controlling the production process, modular construction significantly reduces waste and energy use. Some companies are even building renewable energy systems and smart technology directly into the modules, creating buildings that are not only efficient to construct but also to operate.
Modular architecture has evolved alongside society’s changing needs, offering a smart, flexible way to build that’s become more important over time. In 19th Century as mass production took off, prefabrication allowed for faster and more efficient construction. This gained pace in the mid-20th Century After WWII, as these modular housing helped rebuild cities quickly. In California, Eichler Homes showed how prefabricated design could bring stylish, modern homes to the middle class, making it more egalitarian. This was followed by the Era of 1960s–1990s Architects like Richard Rogers and Norman Foster took modular systems to new heights. Their work, like the Centre Pompidou in Paris, used exposed, modular components not just for speed but to celebrate technology in architecture.
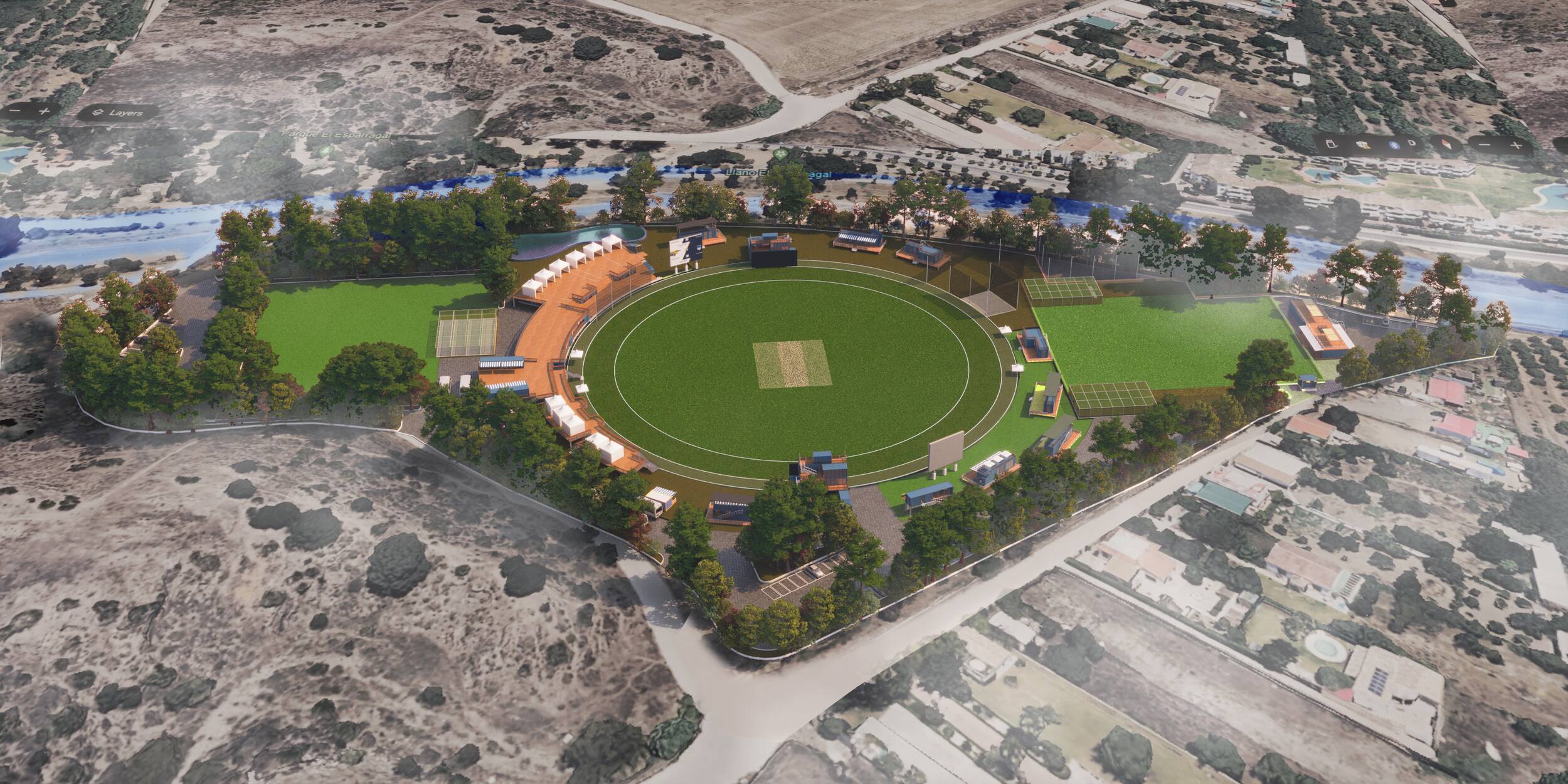
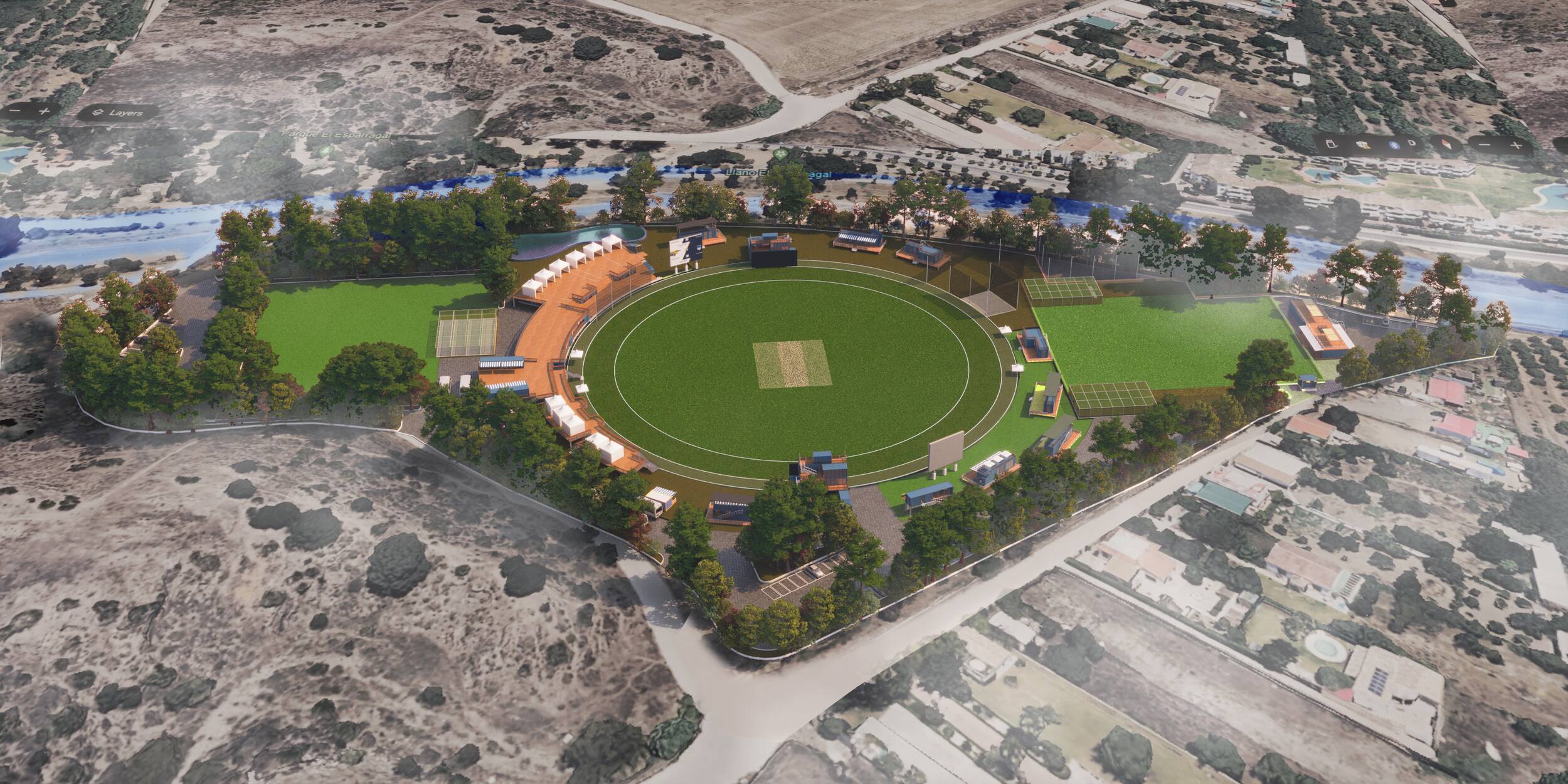
Today, modular architecture is all about sustainability. Prefabricated buildings, including modular skyscrapers, help cities grow while cutting waste and speeding up construction. The use of digital has speed up this by adding more precision, customization, and sustainable designs. Modular architecture has come a long way from its early days. Now, it offers sustainable, adaptable solutions for cities that need to grow smarter and faster. It’s a blend of practicality and creativity, offering a glimpse into the future of how we build.
Modular architecture has great advantage when it comes to timeline. The construction process is very quick and the on-site assembly can take place simultaneously with the foundation work, hence reducing the build time significantly. Prefabrication in a controlled environment reduces labour costs, minimizes material waste, and allows for bulk purchasing, making modular construction generally more affordable. Constructing under a factory setting ensures that materials are protected from weather conditions, and the production process is standardized, resulting in higher-quality construction. Also, Modular construction generates less waste and can be more energy-efficient. Modules can be designed to be reusable or recyclable, and off-site construction reduces noise, pollution, and disruption in the building’s surrounding area.When constructing Modular buildings, it can be easily expanded or modified by adding or rearranging modules. This flexibility allows for future growth or changes with minimal disruption.
As every coin has two sides we there are some disadvantages as well for modular architecture:
Although modular architecture is increasingly flexible, it can still be challenging to achieve highly customized designs. Buildings often need to adhere to standard module sizes as per codes, limiting creative freedom in complex or irregular designs. Prefabricated Modules need to be transported to the site, and the logistics of moving large sections can be expensive and complex, especially for remote or hard-to-reach areas. Transporting such prefabricated structure in a mixed use high density development can be challenging. The upfront investment in prefabrication facilities, specialized equipment, and skilled labour can be high, especially for smaller projects. Since most of the construction is done off-site, it may reduce the opportunity for local contractors and labourers to participate in the building process, which could be a disadvantage in certain communities.
While considering the vide variety materials that go into modular architecture, their selection is based on their durability, sustainability, ease of prefabrication, and energy efficiency. Steel is one of the most popular materials in modular construction due to its strength and flexibility. It is often used for the structural framework of modular units.
Precast concrete panels and blocks are frequently used in modular buildings, especially for walls, floors, and foundations. Wood, particularly engineered wood products like cross-laminated timber (CLT) and laminated veneer lumber (LVL), is used for framing and panelling in both residential and commercial modular buildings. Glass is widely used for windows, facades, and skylights in modular buildings. Plastics, such as polyvinyl chloride (PVC), and composite materials are often used for cladding, insulation, roofing, and interior finishes. Materials like expanded polystyrene (EPS), mineral wool, and spray foam insulation are used to improve thermal performance in modular buildings. Aluminium is often used in window frames, doors, and curtain walls in modular structures, since it can be easily fabricated into custom shapes and adds a modern aesthetic to buildings. Gypsum board, also known as drywall, is commonly used for interior walls and ceilings in modular units.
Modular architecture is increasingly being used in stadium construction due to its flexibility, speed, and cost-effectiveness. Modular components allow for quick assembly, disassembly, and even relocation, making it ideal for temporary or rapidly expanding sports venues. These designs also offer adaptability, allowing stadiums to be easily reconfigured or expanded as needed.


Some well-known modular stadiums are
- Qatar’s Stadium 974 (FIFA World Cup 2022) which is made from 974 recycled shipping containers It was built for the FIFA World Cup and is designed to be fully dismantled and reused after the event.
- The temporary basketball venue for the London Olympics was built using modular components. The 12,000-seat structure was designed to be dismantled after the Games and either reused or recycled.
- The Baku Crystal Hall (Azerbaijan) was Originally built for the 2012 Eurovision Song Contest, this multipurpose venue was constructed using modular techniques, allowing it to be reconfigured and repurposed for sports events like boxing and volleyball.
Using shipping containers as modular architectural components in stadiums has become a popular trend due to their versatility, strength, and cost-effectiveness. Containers offer a ready-made, stackable structure that can be easily transported, assembled, and even reused or relocated. Shipping containers can form the main structural framework of the stadium. Their inherent strength allows them to support seating decks, platforms, and other stadium features. They can be seen being frequently transformed into enclosed VIP boxes, lounges, or hospitality areas within stadiums. Their boxy shape and durability make them perfect for luxury suites, press chambers, or media rooms. Additionally, shipping containers can be used to house restrooms, food and beverage kiosks, and merchandise stores. They offer enclosed, secure spaces that can be quickly equipped with utilities and finished for public use.